Closed Enrollment
Published Course
ReCon Energy in Small Component Systems
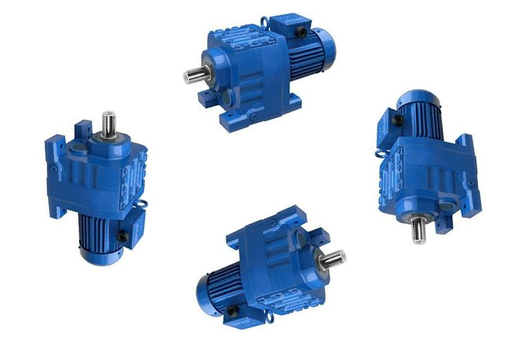
ReCon Energy in Small Component Systems
About this Course
How much do you know about the motors in your plant? This course provides tools and insights to ReCon Leaders to better be able to measure and limit the motor ownership costs, improve motor management strategies, and increase efficiency of gear boxes and belts. By the end of this course, after using tools like MEASUR and the Motor Savings Calculator, ReCon Leaders will be able to partner with maintenance departments and propose tangible policies to improve motor efficiency and reduce costs at their plants.
Course Features
-
100%
Accessible from Any Device
-
Self Directed
Learn with a cohort but when it fits in your schedule
-
On-demand Video
Interactive Video Lessons
-
PepsiCo Internal Expertise
Brought to you by Global Sustainability Operations
What You Will Learn
- How to Calculate and Lower Motor Ownership Costs
- Efficient Motor Management
- How to use the MEASUR tool
- Gear Boxes and Belts Management
- Increasing Motor Savings
- Best Practices
Course Overview
5 Lessons
28 Activities
5 Discussions
2 Live Events
Welcome to the Course
-
Getting Started
-
Attend: Kickoff Call
-
Join this kickoff call to learn about:
- Welcome to the course!
- What to expect in the course
- Downloading/using MEASUR tool
-
Complete or Update: Your Profile
-Take a few minutes to update your profile if needed with any new role, plant, or hobbies so your cohort can get to know you!
-
Reflect: Plant Motor
-Take a short walk around your plant. Where is your oldest small motor? If you aren't sure, ask around! Type your answer below.
-
Discuss: Motor Replacements
-Are you improving efficiency each time you have a motor replaced?
Why or why not?
-
Energy in Small Component Systems
-
Cost of Ownership
-
Watch: The Importance of Efficiency
-This video by ABB Motors and Generators explains the importance of high motor efficiency and mandatory minimum efficiency levels for electric motors. Are there any surprises?
-
Download and Watch: Life Cycle Cost
-Take a look at this Life Cycle Cost intro video. Lauren Baldwin, from University of Texas El Paso, explains the life cycle costing process which is now used by many companies in product design and development.
After watching the video, download the Lighting 101 Document Magazine and take a read.
-
Read: Efficiency Measurements
-Take a look at the below graphics to understand how efficiency standards have evolved worldwide.
Look closely at the new rules for motor efficiency in the table below.
See the chart below for IE Classes for 50 Hz 4-pole motors. Is it what you expected?
-
Watch: Calculating Electric Motor Ownership Costs
-Watch this short video by ABB Motors and Generators on how to calculate electric motor ownership costs and the different factors that contribute to the total cost of ownership.
-
Read: Ways to Increase Efficiency
-Increasing motor efficiency can be achieved a few ways. Take a look at the diagram below and start to think how the methods would apply to your plant.
-
Watch: How to Lower Cost of Ownership
-Take a look at this video by ABB Motors and Generators on how to lower the cost of ownership.
-
Discuss: Factors for Motor Repair
-Now that you know the huge difference increasing efficiency makes in terms of the cost of ownership, what are all the things you would need to consider when deciding to repair or replace a small motor? Return to this discussion throughout the day to get inspiration from other plants.
-
-
Motor Management
-
Read and Download: MEASUR Tool and Guide
-Some of the activities you'll be completing as part of this course will be in an app called MEASUR. The US Department of Energy developed the app to aid manufacturers in improving the efficiency of energy systems and equipment within a plant.
The tool is designed for industrial energy coordinators, plant managers, engineers, and personnel who are interested in improving system efficiency and measuring potential savings opportunities in both dollars and energy savings.
Here is the link to download MEASUR and attached is the download/user guide if you'd like to take a tour before needing the tool for the class.
If you have any difficulty with the download or installing the software, contact PepsiCo IT for assistance.
Feel free to take a few minutes to explore the functions MEASUR has for motors:
The download instructions are attached below.
-
Read: Motor Nameplates Before and After 2011
-Look at the examples below to learn how motor name plates have changed over time.
Nameplates pre-June 2011
Nameplates post-June 2011
-
Watch: Reading Motor Nameplates
-In this video, Jeff Simpson from Jade Learning explains how to read motor nameplates and what particular information they include.
-
Read: 3 Steps to Motor Management
-This is not a comprehensive plan, but it is a good place to start to help you determine cost savings that an effective motor management plan can generate.
1. Establish a motor specification and purchasing policy for new motors
A clearly defined “New Motor Purchasing Policy” is key to effective motor management. Specify top quality motors for performance, reliability, and efficiency, bearing in mind any specific site requirements and operating conditions.
2. Determine a cost-effective repair/replace plan
The traditional perception is that it is more cost-effective to repair a failed motor than to purchase a new one. Many users are surprised by what they find when they take the time to calculate the breakpoint below which it is more advantageous to simply replace a motor and take advantage of the enhanced performance and reliability that comes with the latest technology. The main benefit, however, comes from knowing what you are going to do before a motor fails so that you can make a logical decision and be prepared to act upon it.
3. Define and document appropriate repair standards
Once the decision has been made to repair a failed motor, it is important to know that you are dealing with a thorough, reliable, and professional repair facility. Often, a repair facility can do as much harm as good (particularly when handling rushed repairs) if they do not follow proper procedures. Insist on adherence to a documented repair standard (e.g. AEMT/EASA) to be sure that you are maximizing the return on the investment you’ve made in the repair.
Define your Motor Replacement Strategy
-
Watch: Electric Motor Aging
-How much do you know about the aging of your electric motors? This video by ABB Motors and Generators covers 4 dominant factors impacting aging: thermal, electrical, ambient, and mechanical stress.
-
Watch: Maintenance Strategy
-What is your plant's current maintenance strategy? Watch this video, and take note of any similarities or differences with your plant's strategy.
-
Discuss: Efficiency Changes
-In your opinion, what actions would you need to take to begin making efficiency changes in your plant?
-
-
Motor Savings Calculator
-
Download: Motor Savings Calculator
-Download the Motor Savings Calculator. This calculator will help you evaluate the benefits of high efficiency motors over time and can be used to help you make a business case for replacing older motors with more efficient ones.
Save the below as an Excel Template file type and then you can reuse the template as needed. It is also available at this link.
-
Collect: Motor Activity Information
-Select one of the oldest motors in your plant, or the one you identified in the beginning of this course. Note the motor size, efficiency, weekly run time, and the current cost of electricity for your location. Use this, plus information about more efficient motors you researched, to fill out the first tab of the Motor Savings Calculator.
-
Submit and Discuss: Motor Savings Discoveries
-In the discussion, share what you discovered from filling out the first tab of the Motor Savings Calculator. Any surprises? Use the paper clip below to submit your Motor Savings Calculator and share it with other plants. Check back to see what other plants have submitted and respond to their discoveries.
-
-
Gear Boxes and Belts
-
Read: Worm and Helical Boxes
-This chart shows what factors contribute to gear box unit losses. Continue reading below to learn about worm and helical gear boxes.
Worm boxes are usually recommended for hoisting purposes such as roller shutter door applications. They have sliding surfaces but they can have higher friction. One or two teeth at a time are in contact with another gear, which can create high noise. Worm gears are less expensive to manufacture, but they typically last about three years before they need to be replaced. They are typically not worth repairing.
Helical gearing is machined to have angled teeth that are hardened and ground to achieve an efficient gear mesh. The teeth angle enables the gears to gradually mesh. Thus, two or three teeth of each gear are always in contact with other gears. This configuration lessens the load on each tooth and creates a smooth transition of forces from one tooth to the next. The result : less vibration, wear, noise, and a longer life. These are typically worth repairing.
-
Read: Drive Mounting Positions
-The mounting position of the gear unit plays a role in efficiency because it determines the amount of oil in the gear unit. In the diagram below, the best position is M1 then M2/M3. It's important to have more oil in the box to lubricate the bearing at the highest point. Oil flow is determined by the oil temperature and viscosity. The more viscous the oil, more torque is required to move the gear - the machine is working harder and is less efficient.
-
Download and Review: Drive Belt Information
-Download and read through the information on drive belts in the attachment.
-
Read and Watch: Flow Control Methods
-Throughout a manufacturing facility, we will encounter processes that need flow control to accomplish certain tasks. Examples include the daily cycle of hot water that needs to be pumped and used in sanitation activities, the varying process demand for a liquid, or seasonal heating and ventilating demand. However, the variation required may be in the pump of fan head, such as for cyclical changes in process pressure, or pumping to tanks with a variable liquid level.
In spite of these variations, the pumps and fan capacity are selected to meet the maximum flow and head or even sometime for future needs and perhaps a certain safety margin.
The average pumping capacity may be only a fraction of the maximum capacity and will require some kind of control.
There are several different methods to match process requirements.
A. Throttling
Throttle control is the most commonly used method. The flow caused by the constant speed pump is reduced by increasing the losses in the system by closing the valve.
B. Bypassing
Although not commonly used, bypassing is applied mainly to circulation pumps. The flow output to the system is reduced by to the pump suction.
C. On-off control
On-off control is often used for tasks such as keeping the pressure in a tank between preset limits. The pump is either running or stopped. The average flow is the relationship between the “on” time and the “total” time (on+off).
D. Variable Speed Drive (VSD) also known as Variable Frequency Drive (VFD)
Changing the speed of the pump moves the pump curves in accordance with the affinity laws. If the pump impeller speed is reduced, the pump curve moves downwards. If the speed is increased, it moves upwards. This means that the pumping capacity is exactly matched to the process requirements.
Choose Your Control Method
The below video by ControlTrends illustrates the use of variable frequency drives on pumps and fans in a commercial building setting.
The chart below illustrates the flow percentage required for energy savings. Note that in these curves the pump, motor, and drive efficiencies are also taken into account.
-
Read: Before and After Example
-Take a look at these before (left) and after (right) photos. Is there anything in particular that you notice based on what you have learned in this course?
-
Discuss: Using the MEASUR tool
-How can you use the MEASURE tool to identify opportunities?
-
Capstone
-
Attend: Capstone Call (30:00)
• Recommended for: ReCon Point Person, Maintenance Mechanics, Process Engineers, Process Improvement Engineers, Project Engineers, Regional Leaders
• Prerequisites for this course: ReCon Basics
For 2022, this course will be offered starting August 29, 2022. Register here at least a week prior to the start of the course. Please keep in mind your schedule and time commitment required prior to registration.